驚きと感動の5S活動発表会とは
5S+ Speed、Safety
昨年からお世話になっている多治見市のタイルのトップメーカーさんの
7Sカイゼン活動の発表会が2月にありました。
7Sとは5SにSpeed、Safetyを加えたこの会社様独自のものです。
普段、泥や埃まみれになりながらがんばって作業されてる皆様が
この日だけは、ビシッとネクタイして堂々と発表される素晴らしい場でした。
以下に学びの一部をご紹介します。
【すごい総務】
- 献身的な共有エリアの5S。
駐車場、トイレ、ガーデン倉庫、共用スペースを全員で協力して地道な取り組み。
ガーデンに落ち葉が無い!銀行の支店長も驚き。
多くの会社が、外部委託する清掃、芝生手入れを自分たちでやってしまう。 - ファイルのとりだし。外部駐車場使用料、事務用品削減などで年間250万円削減。
「すべての書類を1分で」「わかる書類は45秒」総務の5S目標がフロアの他職場にも展開。
【企画業務】
- ひととおりの5S改善では物足りず。
「生まれ変わる」もう一度全員ですべての場所を見直し。
何度も現状把握をくりかえして、全員で広範囲のエリアを対象にカイゼンを繰り返し。
年間100万円越えの効果金額。 - でも一番変わったのが「7Sへの意識」
もっと良いやり方が必ずある。
トヨタでは「改善後は、改善前」の言葉があるのを思い出しました。
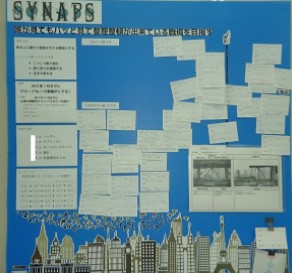
【海外営業】
- ファイルの置き場と表示を見直すことで「探す」「取りに歩く」が減り、「棚の引出し開閉回数」が1/4以下に激減。
同時に工作室の見える化と省スペースで作業性向上。 - 「検査室」が「見本室」になってが空っぽ。驚き。
- ゴミ箱の捨てるライン表示⇒養生プラダンのゴミ箱に変える
「一次改善、二次改善・・」
【製造の5S】
- 「ムリです」と言っていた中国語カイゼンボードが出現。
意見を出そう。できるか、出来ないかでなくて。協力してやろう!
現場の全員が中国語で地声で堂々と発表。
材料、仕掛り品、型や副資材を整理し空間をつくりだし作業性向上。
わかりやすい看板表示で、取り出しやすく戻しやすい工具の置き方改善で時間短縮。
年間100万円以上削減。
無形の大きな効果として主体性、仲間意識の向上。中日友好を祈念。
- 生産や注文指示を必要数に近づけて薬品、生産余剰、保留品を激減させて年間150万のコスト効果。
生産や注文指示ルールで後戻り防止。 - 製品の中間在庫を300万円削減。
フォークリフトで「どかす」をなくすように在庫置き場の区画線を引く。
コスト効果年間140万円。
- 出荷前の清掃短縮 コスト50万円減。溶剤使用量 16万円減。
棚卸し4人かけていてたのが3人でできる。
【物流倉庫】
- 出荷場の集荷便用の文字表示に赤色縁取りをした。
集荷便の人も感動。「わしらのために表示してくれたのか?文字が浮き出て見える」
ちょっとした一工夫が感動を呼ぶ。
全員がその気持ちで仕事したら、その総和はすごいことになる。
- モデルロケーションの5S。整理整頓して探す時間ゼロ。
- 荷時間の星取表(勝ち負け)11月5勝14敗 から 12月は10勝1敗に!
商品のありかを尋ねられる回数82回⇒5回。出荷時間114分⇒23分
3段積み⇒2段積み。ヒヤリハットゼロに。
パレット数153個減。
年間160万円コスト効果。
全員がひとつの方向に向かって、「愚直に実践」するとこんなにも大きな成果が出るんだと再認識させられました。
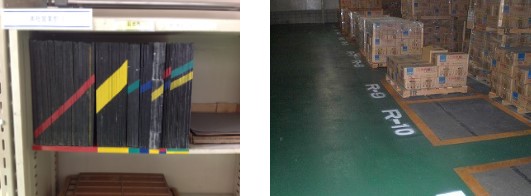
5Sについて詳しく知りたい方は以下にご登録ください。
無料メルマガ「人が育ち現場の力を高める5S活動の進め方」
・なぜ5Sすると業績が上がるのか?
・5Sとは何か?
・儲かる5Sのポイントは?
・組織的な5S活動の取り組み事例
・5S活動を続けるポイント など
全11回のメールセミナーでわかりやすくお伝えしていきます。